Your Local Experts For
Electrical Testing and Tagging
The easy way to make sure your workplace is Safe & Compliant with AS/NZS 3760:2022. Contact our team 24 hours per day.
- 100% Satisfaction Guarantee
- Competitive Pricing
- Full Report & Certificate of Compliance
- Peace of Mind
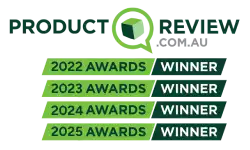
Electrical Test and Tag &
Fire Testing and Tagging Experts

Fast & Efficient

Over a Decade of Experience

Comprehensive Reporting

Franchises Available

Giving Back
Learn more here.
Why Choose The Local Guys – Test and Tag
Dreaming of Franchise Ownership? Let's Get You Started!
franchise opportunitiesWe Offer Our Services Across Australia
Portable Appliance Testing
Portable appliance testing, ensures the safety of movable electrical devices. It involves two steps: visual inspection and electrical testing with a Portable Appliance Tester (PAT). This electronic test determines if the appliance is safe, providing a pass or fail result. It safeguards workplace individuals from electrical hazards like fires and shocks, promoting device longevity.
Safety Switch (RCD) Testing
RCD testing, also known as Residual Current Device testing, verifies the functionality of safety devices in electrical circuits. This involves testing the Residual Current Device (RCD) to ensure it effectively detects and responds to electrical faults, such as leakage currents. RCD testing helps prevent electric shocks and reduces the risk of electrical accidents.
Fire Extinguisher Testing
Fire extinguisher testing ensures the effectiveness of this vital firefighting tool. Merely having a fire extinguisher is insufficient; it must be in proper working condition. A malfunctioning extinguisher during an emergency can escalate a manageable fire into a dangerous situation. Conducted by professionals, testing includes visual inspections and integrity tests, documented in detailed reports.Â
Emergency Exit Light Testing
Emergency exit light testing verifies the functionality of crucial evacuation lighting systems. These lights guide occupants to safety during emergencies, such as fires or power outages. It ensures that exit routes remain clearly illuminated, facilitating safe evacuation. Testing involves inspecting and testing emergency lights to confirm they illuminate adequately and remain operational. Compliance with relevant safety standards, such as AS/NZS 2293.2:2019, is essential to ensure the effectiveness of emergency exit light systems.
Fire Blanket Testing
Fire blanket testing ensures the reliability of critical safety devices designed to extinguish small fires or smother flames on a person's clothing. Proper testing confirms that fire blankets deploy effectively and can withstand the heat of a fire without damage, ensuring their readiness in case of emergency. Conducted by trained professionals, testing typically involves visual inspections and integrity assessments, adhering to relevant safety standards to uphold effectiveness and compliance.
Microwave Leakage Testing
Microwave leakage testing ensures the safety of microwave ovens by detecting and measuring any radiation leaks. This crucial safety measure helps prevent potential harm to users and ensures compliance with safety regulations. Conducted using specialised equipment, testing involves assessing microwave emissions to verify they are within safe limits. Regular testing by professionals helps mitigate risks associated with microwave radiation exposure, promoting a safer environment for users.
$5 from every job gets donated
to World Vision Australia
giving back initiativesHow it works, getting started is easy

STEP 1. QUOTE

STEP 2. SCHEDULE

STEP 3. PERFORM TEST

STEP 4. SIGN OFF
Read What Our Customers Have To Say
We offer our services Australia wide
Request a QuoteFrequently Asked Questions
Electrical test and tagging is the process of checking the safety of portable electrical appliances. This service is completed as a precautionary safety measure to ensure that the appliances used at a workplace are safely operating and in good working order. The purpose of test and tagging is to prevent (or reduce the risk of) electrical hazards, such as electrical shocks and fires.
Test and tagging consists of four parts:
- Visual inspection – The item is visually inspected for any damage or faults to the appliance or cord. The appliance must visually be in good working order to pass the test.
- Electrical Test – Using a Portable Appliance Tester (PAT), we electronically test the item to determine if it is functioning correctly.
- Tagging the item – The item will be labelled with a company tag to signify that it has been tested. This tag will include the test date, due date and the technician’s licence number. If the item fails the test, it will be tagged with an ‘Out of Service’ tag to clearly show the item is unsafe for use.
- Reporting – You will receive a completion report outlining the items tested, failed items, recommendations, due dates, etc.
As per Occupational Health and Safety requirements, businesses are required to ensure a safe work environment. Employers are required to take all reasonable steps to provide a safe, hazard-free workplace, which includes having an electrical maintenance plan to uphold their duty of care. The AS/NZS 3760:2022 Standard outlines that regular testing and tagging of electrical appliances is optimal for creating a safe workplace.
All test and tagging is completed in line with the AS/NZS 3760:2022 Standard. Testing for construction, demolition and mining is also completed in accordance with the AS/NZS 3012 Standard.
In addition to ensuring your business is compliant with the Australian testing standard, having regular electrical test and tagging completed assists with insurance claims, liability claims, and even acts as an asset register of your electrical equipment. It also offers peace of mind, knowing your electrical equipment is safe.
The list would be too long to name every item that can be tested! The best way to narrow this down is that anything that can be plugged into a standard power outlet needs to be tested. This includes Class 1 and Class 2 items. Common appliances that are tested include extension cords, chargers, electric drills, fridges, printers… and the list goes on.
Any items that are used at the workplace should be tested and tagged even if they are not company-owned. This includes any personal items from home that are brought into and used at the workplace.
Yes! All our technicians are mobile. This means we will come to you to complete the work, so there is no need for you to worry!
Test and tagging is a relatively quick service. The process includes a visual inspection and an electronic test using a PAT (portable appliance tester). We do need to inspect the appliance and plug the appliance into the PAT; therefore, the equipment will need to be out of use for a couple of minutes while we complete the test. However, our technicians will always do their best to make the process as smooth and interruption-free as possible. Before turning off any equipment that is in use, our technicians will always ask for your permission first.
Yes! We have many clients that we service on a national scale. These include government buildings, university housing facilities, medical and radiology clinics, service stations, national franchise chains and many more. We have franchise partners in each state, so this is no issue for us! Our team will assign you a project manager at our support centre who will be your point of contact, so you do not need to worry! We will manage the whole process in an easy and stress-free way.
A Residual Current Device (RCD), commonly known as ‘safety switches’, is a safety device that is designed to ‘trip’ (immediately turn off power to the circuit it is attached to) when it detects the electricity is leaking to the earth at a potentially dangerous level. The purpose of an RCD is to prevent the risk of electrical emergencies. However, an RCD will only protect you if it is working correctly, which is why we conduct RCD tests to ensure this.
RCDs are designed to be very sensitive, therefore, many different factors (such as dust build-up, damage, old age and poor quality) can hinder their functionality. RCD testing includes two different tests. Push-button tests are completed every 6 months and check if the RCD trips. Timed tests are completed every 12 months and check how quickly the RCD responds to a surge in power.
All RCD testing is completed in line with the AS/NZS 3760:2022 Standard.
It is common for people to refer to the service as tag and test, however, the correct name is test and tag. The words ‘test and tag’ clearly outline the process of the service. First, we test the appliance and then follow by tagging it.
As per the AS/NZS 3760:2022 Standard, electrical test and tagging must only be completed by a ‘competent person’ in Australia. To be deemed as competent, an individual needs to gain a test and tag licence by completing the relevant test and tag course.
At The Local Guys – Test & Tag, all technicians are fully qualified and complete ongoing company training to remain up to date and proficient in the latest skills and industry knowledge.
The frequency of test and tagging varies depending on the environment you are in.
- Construction, demolition and mining must be completed every 3 months
- Workshop and manufacturing must be completed every 6 months
- Office environments is to be completed every 12 months to 5 years
If you are unsure how often you should have your test and tagging completed, feel free to have a chat with one of our qualified technicians.
An electrical test and tagging service with The Local Guys – Test & Tag includes:
- A mobile service, meaning the technician will come to your business or location to complete the service
- Testing and tagging the appliances (which includes a visual inspection of the appliance, an electrical test using a Portable Appliance Tester (PAT) and the tags)
- Comprehensive Reporting which lists all items tested, applying a barcode, asset number, and location and indicating whether they passed or failed. For any items that do fail, we explain why the item failed and what action has been taken.
- Certificate of compliance
- Follow up reminders to notify you when your testing is due next (one less thing you need to remember and worry about!)
- Customer Online Portal where you can access all your documents, notes, invoices, etc in one centrally managed location
All franchise partners at The Local Guys Test & Tag are required to have the following current clearances and certificates:
- National Police Clearance Check
- Working with Children Check (WWCC)
- White Card
- First Aid Certificate
- Test and Tag Licence
Our Support Centre keeps a record of all franchise partner’s certificates, clearances and expiries to ensure they remain up to date.
All our franchise partners have $20,000,000 in Public Liability Insurance to ensure they are completely covered in the event of an incident. Evidence of insurance can be provided to you upon request. Our franchise partners also have Work Cover in the instance of an injury. These insurances ensure that both our franchise partners and everyone throughout your business are safe and protected in the case of an incident.
If an item fails the test, a few things will happen. First, we will place a Failed/Out of Service tag on the item, so it is not mistaken as a safe item.
The technician will also notify you of the failed item and discuss with you how this may be rectified. This will vary case by case depending on the item and the issue. For example, if it is a damaged extension cord, our technicians may offer to remove it from the site and correctly dispose of it. If it is a bigger or more expensive item, like a refrigerator, the technician will notify you and provide a recommendation to rectify the issue (such as seeking out an electrician or a refrigeration mechanic to fix the problem).
Lastly, we will provide you with a comprehensive report, including an asset register of the items, indicating the failed items, where they are located and what action was taken.
Yes and no. When you purchase a new item, you do not have to have it tested to bring it into service. However, the item does still require a 'new to service' tag. This tag must include the date that the appliance was purchased or first brought into use. A new to service tag can be installed by anyone and can be purchased through an electrical supplier. This tag will remain valid for 12 months or whenever the next round of electrical test and tagging is due (whatever one comes first).
New items do not need to be tested before adding the new to service tag because there is an expectation of manufacturers to only sell products that are deemed safe. However, in saying this, we regularly see new items that are faulty or have been recalled. Therefore, we still recommend you have your new items tested and tagged to prevent these risks.
Speak to a Real Person Immediately
- Instant, personalised assistance from a friendly voice.
- Tailored recommendations based on your budget and requirements.
- Enjoy the flexibility of customising the scheduling of your electrical safety service.
